This multiphysics model examines temperature and heat induced stresses for one braking cycle in a brake disc assembly, and involves coupling of the stress-strain and heat transfer physics modes. The braking process consists of applying a brake pad to the front part of the disc which induces heat through friction, and results in build up of stresses and strains in the brake disc. Both rotational and axial symmetry is used to reduce the computational cost. Simulations have been performed with the geometry and material parameters given in the reference [1] resulting in the final temperature and stress fields shown in the following figures.
The resulting temperature and stress curves on the disk surface at various times agree well with the results computed with the Nastran FEA software [1].
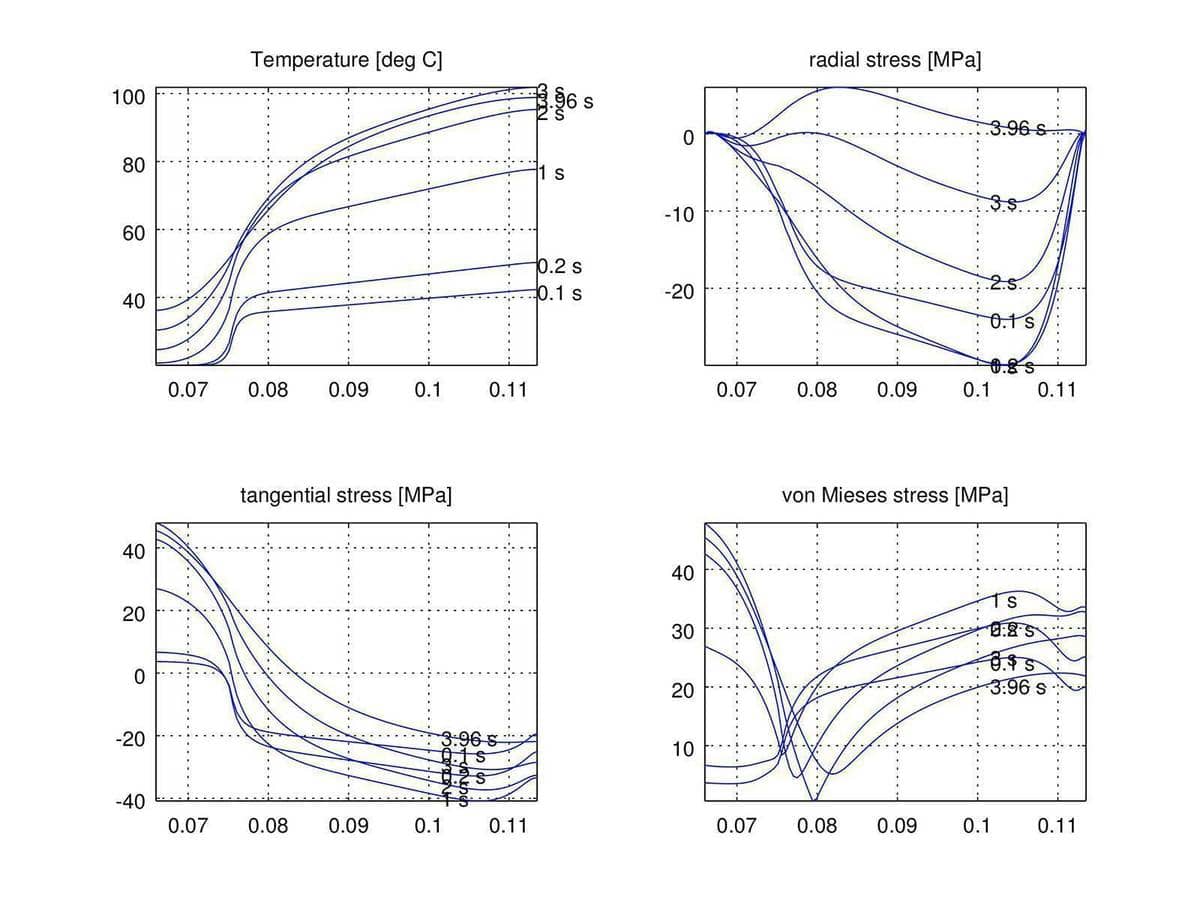
The video below shows how the stresses at various points increase as
the temperature builds up due to friction.
This model is available as an automated tutorial by selecting Model Examples and Tutorials… > Multiphysics > Heat Induced Stress in a Brake Disc from the File menu, as FEATool m-script model file for MATLAB, or alternatively by following the linked step-by-step instructions. In addition, command line postprocessing used to generate the plots is described in the linked post.
Reference
[1] A. Adamowicz, Axisymmetric FE Model to Analysis of Thermal Stresses in a Brake Disk, Journal of Theoretical and Applied Mechanics, 53, 2, pp. 357-370, Warsaw 2015.